What are the process factors that affect the plastic extrusion of the vertical injection molding machine?
(1) Temperature. The temperature has a significant effect on the plastic extrusion of the vertical injection molding machine and the performance of the parison. Increasing the heating temperature of the vertical injection molding machine will have the following effects: it can reduce the viscosity of the melt, improve the fluidity of the melt, and reduce the power consumption of the vertical injection molding machine; the screw speed can be appropriately increased without affecting the mixing and plasticization of the material Effect; is conducive to improving the strength and brightness of the final product; is conducive to improving the transparency of the final product. However, if the melt temperature is too high, the extruded parison will easily sag in its own weight, causing uneven longitudinal wall thickness of the parison; it will extend the inflation cooling time of the parison; it will expand the shrinkage of the final product; it will cause pvc Degradation of other heat-sensitive plastics significantly reduces the parison strength of engineering plastics such as Pc. Therefore, the heating temperature of the extruder should be set according to this principle, that is, under the premise that a smooth and uniform parison can be extruded without overloading the transmission system, in order to ensure a higher melting of the parison. Body strength, lower heating temperature should be adopted as much as possible. When setting the heating temperature of the vertical injection molding machine, the temperature of the feeding section should be relatively low to prevent the material from blocking at the feeding port and affecting the conveying of the material; the temperature of the compression section is higher, which is conducive to the mixing and plasticizing of the material; The temperature can be lower than the compression section, but higher than the feed section, which is conducive to stable and uniform feeding to the die. (2) Melt pressure. The pressure of the melt entering the machine head should be even. Properly increase the pressure of the melt in the vertical injection molding machine to make the materials evenly mixed and stabilize the performance of the parison and the final product. For high-molecular-weight polyethylene, high-density polyethylene and low-density polyethylene blends, and polymers colored with color masterbatches, sufficient melt pressure can make the parison have a good appearance and reduce "crystal points" and clouds. Shaped pattern. However, due to debris blocking the machine head screen, the melt pressure is too high, which will increase the load of the vertical injection molding machine and damage the machine. The screen should be replaced and cleaned in time to keep the melt entering the machine head at a stable pressure. Adopting resins with low melt flow rate, lowering the heating temperature of the extruder, and increasing the speed of the extruder screw can all increase the melt pressure of the extruder. In order to control the extrusion pressure of the melt, a melt pressure measuring instrument can be installed in the discharge section of the vertical injection molding machine. Commonly used instruments for measuring melt pressure include mechanical pressure gauges, hydraulic pressure gauges (silicone oil, silicone grease, mercury), pneumatic pressure gauges, and electrical pressure gauges. (3) Melt conveying speed. If the melt conveying speed is high, the extrusion capacity of the vertical injection molding machine is large. Increasing the conveying speed of the melt can improve the sag of the parison and increase the wall thickness of the parison. The melt conveying speed increases with the increase of the screw diameter, and is less affected by the pressure of the machine head. Increasing the speed and heating temperature of the extruder screw can increase the conveying speed of the melt correspondingly. However, when the screw speed is increased to a certain value, melt fracture is likely to occur. In the plastic extrusion experience of the vertical injection molding machine, the above three factors are mutually influential. At the same time, the volatility of these three factors is required to be small. If the temperature, pressure, and melt conveying speed fluctuate greatly, not only will the wall thickness uniformity and repeatability of the parison become worse, but also the mechanical properties and dimensional stability of the final product will have greater differences and performance. Fell. www.highsun-machinery.com 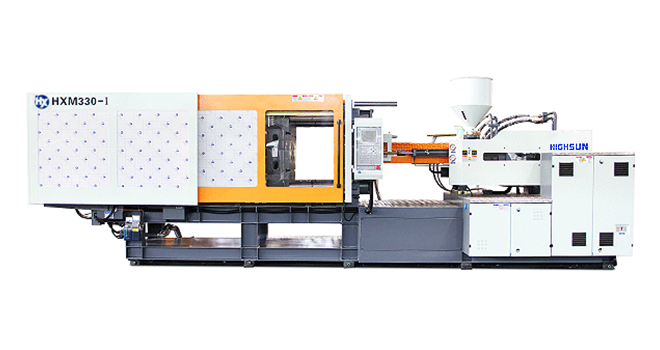
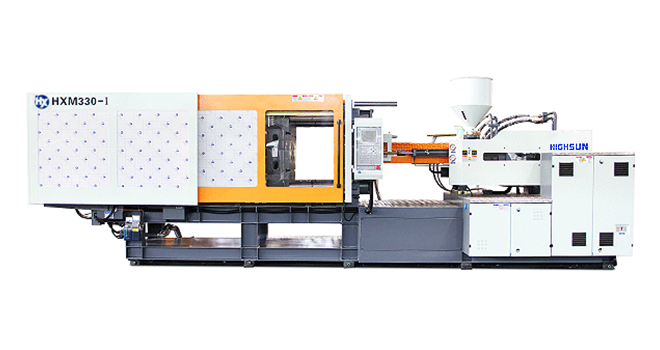