How to deal with the problems encountered in the injection part of the injection molding machine?
1, can not shoot glue
Approach:
1) The nozzle is blocked by foreign objects. Check whether the nozzle is blocked, clean or replace the nozzle.
2) The glue nozzle is broken. Disassemble the flange to check whether the glue nozzle is broken, and replace the glue nozzle.
3) The injection direction valve is stuck. Check whether the directional valve has 24V voltage, and the coil resistance is 15-20 ohms. If it is normal, the valve is blocked. Clean the valve or replace the directional valve.
4) The injection piston rod is broken. Loosen the tight nut of the injection piston rod, check whether the piston rod is broken, and replace the piston rod.
5) The barrel temperature is too low. Check whether the actual temperature reaches the melting point temperature required for the material, and reset the barrel temperature.
6) The oil seal of the injection piston is damaged. Check whether the piston oil seal is damaged and replace the oil seal.
2. The sound of plastic injection is loud at the start
Approach:
1) The injection speed starts too fast. Observe the change in the starting speed of the injection speed, and adjust the injection flow rate.
2) There is air in the oil circuit. Observe whether there is vibration in each action.
3. The sound is loud when the plastic injection is terminated and the melt is transferred.
Treatment method: The action conversion speed is too fast when the glue is injected. Check whether the injection glue has increased the holding pressure, increase the holding pressure, adjust the injection series, and add the glue melting delay.
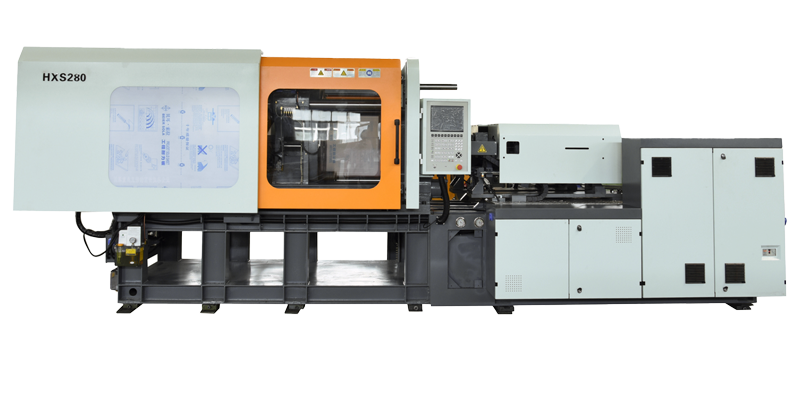
4. The amount of glue injection is unstable
Approach:
1) Cylinder oil seal is worn. Observe the pressure retention of the pressure gauge and replace the oil seal.
2) The rubber nozzle and rubber ring are worn. Detected with 2 injections of glue, replace the three-piece glue dispensing nozzle.
3) The barrel is worn. Use 2 nozzles to detect, disassemble the material to check the wear and tear, and replace the glue barrel.
5. Semi-automatic without glue injection.
Approach:
1) The advance of the launcher is not terminated. Check whether the travel switch in front of the injection table or mold clamping is normal, and check the circuit and travel switch.
2) Disconnect. Check wiring and rewire.
3) Clamping and returning to zero. When the hinge is straight, the position is 0, and the zero position of the electronic ruler is re-adjusted.
6. During semi/automatic operation, the barrel temperature gradually exceeds the set value.
Approach:
1) The melt speed is too fast. Use a tachometer to test whether the screw speed is too fast and reduce the melt speed.
2) The back pressure is too large. Observe the product, the back pressure gauge value, and reduce the back pressure as much as possible.
3) The friction between the screw and the barrel. Remove the screw and barrel, check the wear condition, and replace the barrel or screw.
4) Improper temperature setting. Check whether the actual temperature is too low, and reset the temperature.
5) The shear heat of the plastic is too large. Check the temperature rise in the front section and the middle section, reduce the melt speed and back pressure.
Approach:
1) The nozzle is blocked by foreign objects. Check whether the nozzle is blocked, clean or replace the nozzle.
2) The glue nozzle is broken. Disassemble the flange to check whether the glue nozzle is broken, and replace the glue nozzle.
3) The injection direction valve is stuck. Check whether the directional valve has 24V voltage, and the coil resistance is 15-20 ohms. If it is normal, the valve is blocked. Clean the valve or replace the directional valve.
4) The injection piston rod is broken. Loosen the tight nut of the injection piston rod, check whether the piston rod is broken, and replace the piston rod.
5) The barrel temperature is too low. Check whether the actual temperature reaches the melting point temperature required for the material, and reset the barrel temperature.
6) The oil seal of the injection piston is damaged. Check whether the piston oil seal is damaged and replace the oil seal.
2. The sound of plastic injection is loud at the start
Approach:
1) The injection speed starts too fast. Observe the change in the starting speed of the injection speed, and adjust the injection flow rate.
2) There is air in the oil circuit. Observe whether there is vibration in each action.
3. The sound is loud when the plastic injection is terminated and the melt is transferred.
Treatment method: The action conversion speed is too fast when the glue is injected. Check whether the injection glue has increased the holding pressure, increase the holding pressure, adjust the injection series, and add the glue melting delay.
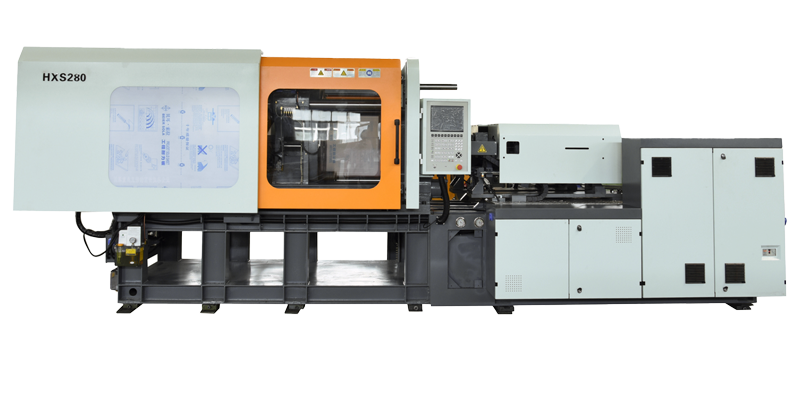
4. The amount of glue injection is unstable
Approach:
1) Cylinder oil seal is worn. Observe the pressure retention of the pressure gauge and replace the oil seal.
2) The rubber nozzle and rubber ring are worn. Detected with 2 injections of glue, replace the three-piece glue dispensing nozzle.
3) The barrel is worn. Use 2 nozzles to detect, disassemble the material to check the wear and tear, and replace the glue barrel.
5. Semi-automatic without glue injection.
Approach:
1) The advance of the launcher is not terminated. Check whether the travel switch in front of the injection table or mold clamping is normal, and check the circuit and travel switch.
2) Disconnect. Check wiring and rewire.
3) Clamping and returning to zero. When the hinge is straight, the position is 0, and the zero position of the electronic ruler is re-adjusted.
6. During semi/automatic operation, the barrel temperature gradually exceeds the set value.
Approach:
1) The melt speed is too fast. Use a tachometer to test whether the screw speed is too fast and reduce the melt speed.
2) The back pressure is too large. Observe the product, the back pressure gauge value, and reduce the back pressure as much as possible.
3) The friction between the screw and the barrel. Remove the screw and barrel, check the wear condition, and replace the barrel or screw.
4) Improper temperature setting. Check whether the actual temperature is too low, and reset the temperature.
5) The shear heat of the plastic is too large. Check the temperature rise in the front section and the middle section, reduce the melt speed and back pressure.