How to choose a fixed pump injection molding machine?
The fixed pump is a type of rotary screw machine and is used to manufacture large numbers of identical parts or products by using a single casing. Usually, the casing is made of steel (although it can be made of other materials as well), and it has a hole for inserting a bolt or screw. As the name implies, the process involves feeding the material either up (the case) or down (the ejector) the mold by means of an ejector with a fixed or adjustable screw. Typically, there is a series of holes, called an injection path through which the material is fed. A fixed pump injection molding machine is usually the preferred choice of most modern manufacturers because of its advantages: low cost, high efficiency, versatility and reliability. Injection molding machines are used in various manufacturing processes, but the most common use is in manufacturing plastic products, particularly those in the automobile or consumer market sector. In fact, many automobiles feature such technology today because they are able to provide the advantage of energy-efficient cars despite the increased cost of fuel and an ever-increasing amount of carbon dioxide in the atmosphere. Because plastic parts are not formed using traditional molds, there are certain advantages inherent in using such machinery, most importantly the savings in production time. The first is the semi-automatic pet preform injection moulding machine. This is mainly suitable for the manufacture of plastic parts that are not complicated in design. The product that can be produced through this machine includes seat belts, side skirts, pet preform bodies, and so on. Semi-automatic machines are normally powered either by electricity or hydraulic strength and are extremely reliable. However, it is important to note that this type of machine is often expensive due to the need to install the electrical pump that controls the movement of the piston inside the cylinder. The second type of machine is the fully hydraulic injection molding machines. These machines are capable of providing high levels of output even when there is a lower level of the required injection pressure. These fully hydraulic machines are normally preferred over the semi-automatic machines because they do not need to exert too much force to move the rod. They provide smooth operation and also ensure that the plastic pieces produced are consistent in shape. A fully hydraulic machine is capable of producing the largest number of plastic parts that are possible to a semi-automatic machine can only manage a certain number. The third type of machine is the toggle pusher or rotary actuator. This type of machine is commonly used for the production of large plastic parts such as buttons, holsters, switches, and so on. The toggle pusher or rotary actuator is commonly used as an instruction or guide system that helps users get the right positioning of the parts. A downside to using the toggle pusher or rotary actuator is that it is comparatively slow in operation and can only handle a limited number of shapes.
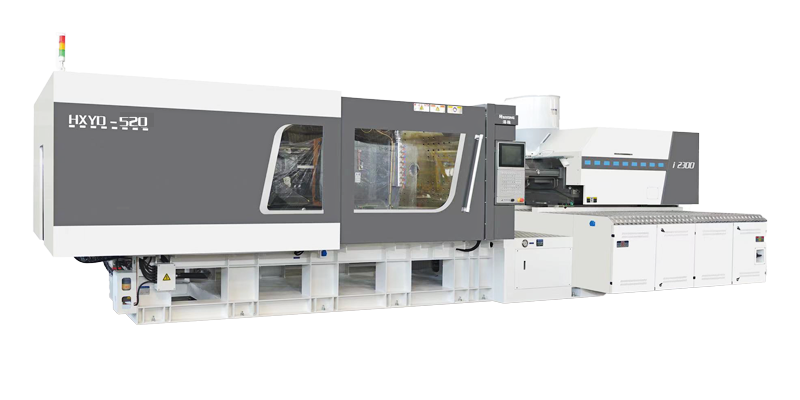